Sorry, it doesn’t look like that page exists.
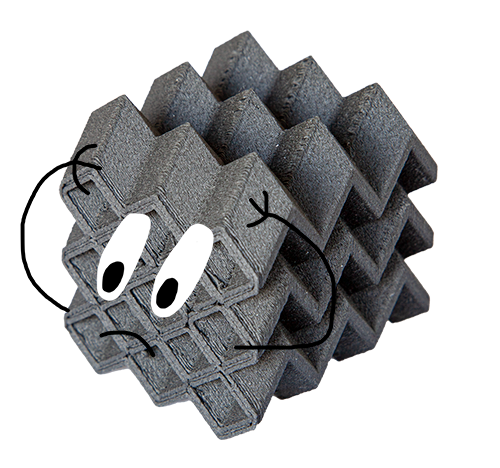
Multiscale Systems
Based in Massachusetts, Multiscale Systems is an industrial solutions company providing technical engineering project management and advanced manufacturing. Our R&D portfolio creates technologies, like metamaterial composites, that provide unique advantages for our customers. We are committed to quality, creative ideation, and collaboration.
Multiscale Systems
Based in Massachusetts, Multiscale Systems is an industrial solutions company providing technical engineering project management and advanced manufacturing. Our R&D portfolio creates technologies, like metamaterial composites, that provide unique advantages for our customers. We are committed to quality, creative ideation, and collaboration.