Companies providing services aboard the International Space Station National Laboratory (ISSNL) have opened a door – or an airlock – to the austere conditions of low Earth orbit (LEO). Multiscale Systems is leveraging this burgeoning market to test the accelerated aging of metamaterials in space, the results of which will support their adoption into everyday products.
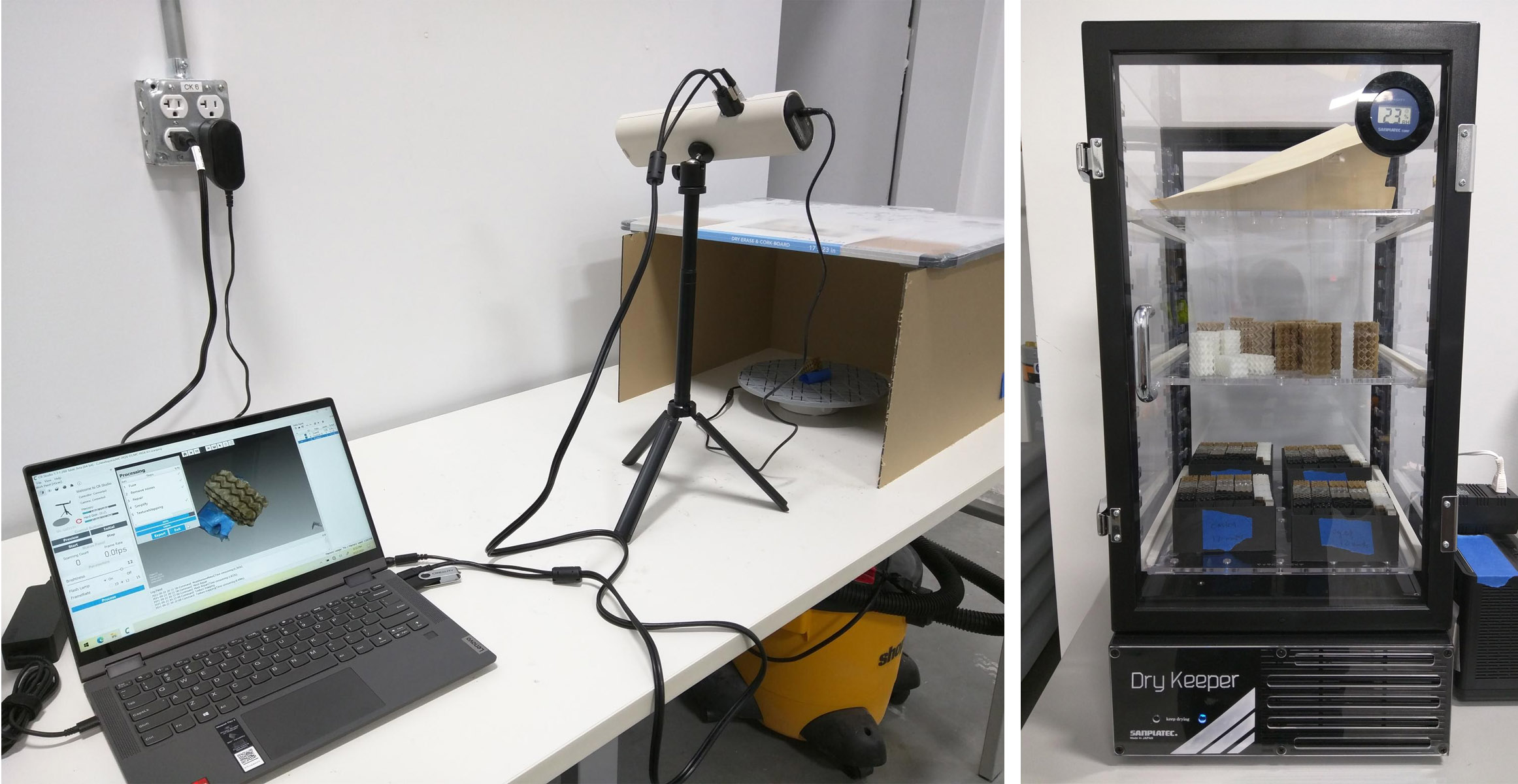
Recording 3D models of coupons (left) and coupons sitting in temperature- and humidity-controlled environment (right). Several sets of identical coupons were created – some to be left on Earth while others are meant to spend 6 or 12 months aboard the ISSNL where the accelerated aging of metamterials will occur.
Exposing anything to ultra-low vacuum, extreme temperatures, radiation, and atomic oxygen for just a few months expedites the aging process. By accelerating the aging of metamaterials we’ll get to play the part of fortune teller, peering into the future to see how our technology will behave 20 years from now. This advanced materials R&D supports product life cycle engineering for industrial applications in a fraction of the time that testing on Earth can provide.
A history of national laboratories
World War II saw a period of public sector investment in basic science that supported a range of inventions, from the earliest computer to the atomic bomb. These investments went to a combination of academic labs and secret government sites to support large collaborations like the Manhattan Project. Having proven their worth in wartime, the U.S. Government later decided to extend their temporary existence into a permanent set of national laboratories for continuing research into physics, chemistry, and materials science.
Today, these national labs are mostly managed by a mix of private companies and academic universities, with elements of both competition and collaboration baked into their culture. Seventeen laboratories are also run under the U.D. Department of Energy (DOE), and a handful are sponsored by other Federal agencies.
Yes, the DOE’s particle smashers are awesome and get most of the headlines, but NASA has a National Lab too, and theirs flies overhead 15.49 times a day in low Earth orbit.
More precisely, the U.S. portion of the International Space Station (ISS) is a designated National Lab, which creates exciting possibilities for the U.S. industrial base. An important feature that distinguishes a National Lab from an academic counterpart is that they’re responsible for promoting innovation that increases U.S. economic competitiveness by advancing research that spans across sectors.
If you work at a satellite communications company or are developing better geographic maps, it’s obvious why you’d want to utilize the ISS National Lab. But the use of ISSNL facilities far exceeds the fantastic view. In fact, it’s a great venue for conducting materials research.
Space as an opportunity for materials R&D
Ever get a bad sunburn? Imagine how much worse all that UV exposure would be if you didn’t have the Earth’s atmosphere protecting you.
How about the feeling of getting into a cold car on a winter morning after it’s spent the night parked outside? Or just as bad – getting into a black car with leather seats that’s been sitting in the summer sun all afternoon. Those extreme temperatures can be pretty brutal.
If you’ve ever lived by the sea or in areas that salt the roads during winter, you’re likely familiar with the corrosive effect of salt – it eats any metal it’s allowed to contact. I can still remember my heart sinking into my stomach when I saw what it was doing to the underside of my first car.
In LEO, the conditions of space have all these effects combined. Extreme UV. Extreme temperatures. And even extreme corrosion by atomic oxygen. And it’s all at once. All the time.
Oh, and don’t forget micrometeoroid impacts, plasma, and cosmic rays.
The point is that the extreme conditions of space take the harshest environments we have on Earth and amplify their effect. From the perspective of an aerospace engineer building satellites or other orbiting systems, the space environment is an obstacle to overcome. From the perspective of materials R&D, this same environment is an opportunity.
Why the extreme conditions of space are perfect for the accelerated aging of metamaterials
When you think about aging, the images that come to mind might include the way human skin responds to excessive UV damage or the way extreme temperatures crack paint. Think about all the added cost of replacing corroded car parts.
A relatively simple thread ties these observations together: environmental extremes induce aging, and extreme environments induce extreme aging.
The austere conditions of space are certainly extreme, and several years worth of aging can be induced by just a few months of space exposure.
Accelerated aging of sample materials with the ISSNL allows us to glimpse the future. Consistent with their mission to promote U.S. economic competitiveness, the ISSNL’s facilities – a relatively simple airlock and some mounting brackets – allow companies like Multiscale Systems to determine how our mechanical metamaterial products will perform after years of real-life use.
Our metamaterials will be exposed to all the wonderfully extreme conditions of LEO for 6 and 12 months, and upon their return to Earth we’ll test and compare them against identical samples left on the ground.
So, when customers ask how we know these materials will last the required 10, 20, or even 30 years, test data on samples returned from orbit provide real answers.
PEEK coupon recorded with the Polycam app to produce a 3D model.
Hurry up and wait
In principle, any business can leverage the ISSNL to launch their products into space. In practice, there’s a lot of elbow grease that goes into getting a project off the ground (literally).
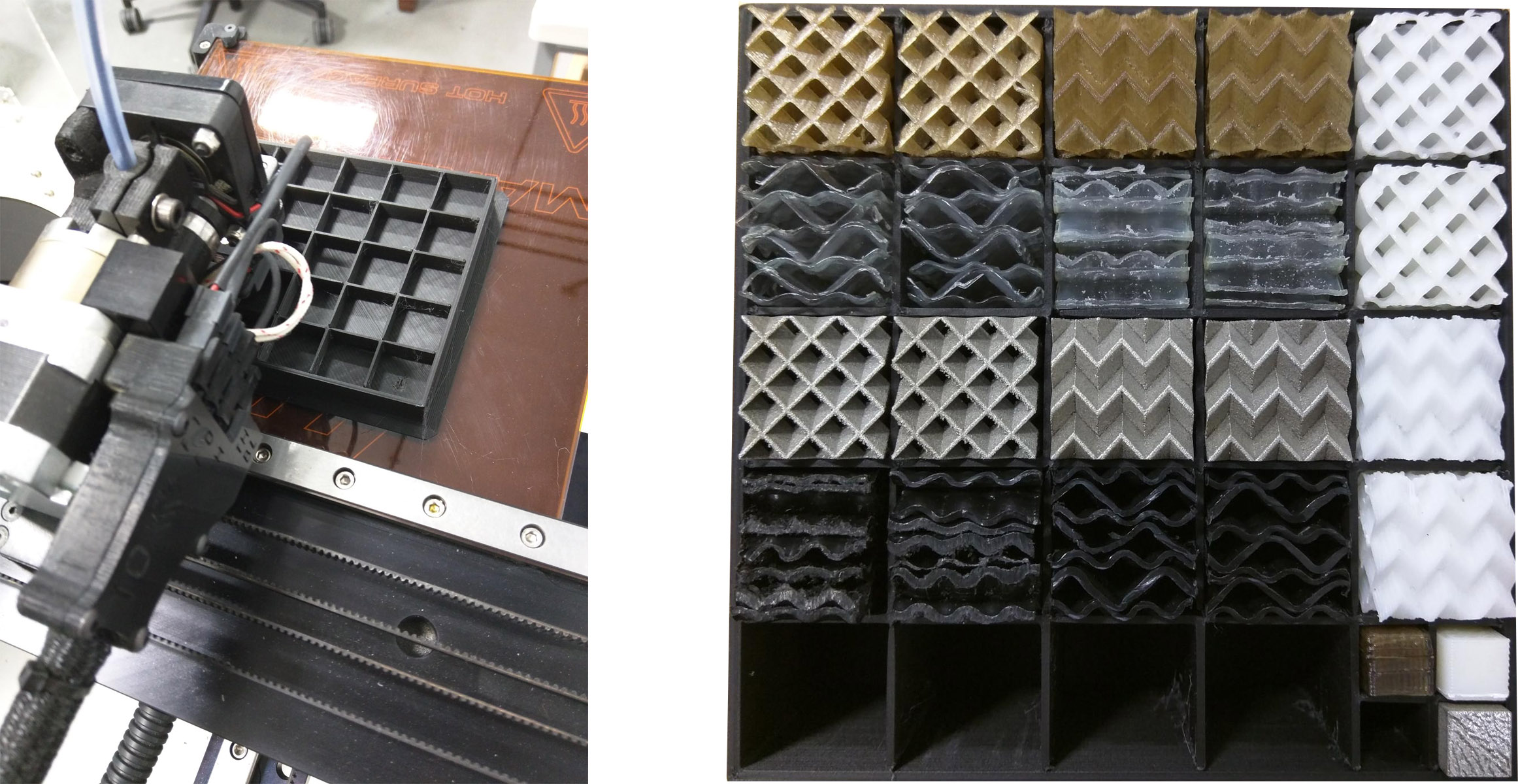
3D-printing of coupon box (left) and the finished box loaded with various coupons (right)
In our case, our team had to design a custom sample container that can withstand the forces, shocks, vibrations, outgassing, volatility, and exposure criteria. At some level, it’s just a box. At another level, it’s a very sophisticated box. But once it was designed and the samples were fabricated, we were good to go.
We also received funding from NASA in the form of a Phase I SBIR, which has allowed us to design, fabricate, and prep our boxes of metamaterials.
With samples destined for an existence of accelerated aging, we sit and wait. While they may only be in space for 6 or 12 months, their return will give us insights into a lifetime of use.
Latest Lab Notes
News /
March 11, 2025 – Multiscale Systems to showcase cutting-edge industrial innovation during StartUp Week Worcester 2025.
News /
Multiscale Systems receives Massachusetts manufacturing award in recognition of outstanding leadership skills in the manufacturing industry.
Press Release /
WORCESTER, Mass. (July 12, 2024) – Multiscale Systems to build new facilities, expand advanced manufacturing capabilities, and bring jobs to Worcester with grant investment.