Climate change is one of the greatest challenges facing the planet and it’s having a profound impact on the natural world. The causes of climate change are complex and multifaceted, but the overwhelming scientific consensus is that human activities, particularly the burning of fossil fuels, are a major contributor.
Addressing climate change requires a global effort to reduce greenhouse gas emissions and transition to a more sustainable and low-carbon economy. To meet these needs, U.S. states have begun phasing out sales of gas-powered vehicles with an emphasis on moving the market toward electric vehicles.
Safety first
Electric vehicles have many advantages over gas-powered vehicles, including their quiet operation, convenient at-home charging and, of course, lower carbon emissions. However, replacing combustion engines with batteries introduces a new set of safety concerns for engineers.
Lithium-ion batteries have a high-energy density and long lifespan, making them a popular choice for electric vehicles. But damage to these batteries can result in thermal runaway, a self-perpetuating reaction in which the battery heats up and releases more and more energy until it explodes or catches fire.
These battery fires can be difficult to extinguish and threaten human life in an otherwise minor car crash. Preventing damage to the batteries is a top priority for engineering safety in all modes of future transportation.
Protecting the battery
To make lithium-ion batteries safe for the road they’re encased in a battery box. Battery boxes mitigate impact forces in the event of a collision and also provide an active cooling solution to prevent thermal runaway.
Challenges with today’s battery boxes
A major challenge in designing battery boxes for electric vehicles is creating a system that is simultaneously lightweight, compact, and low-cost, while still being safe and efficient. Cooling systems keep the battery operating smoothly, but they add weight and create undesired thermal insulation.
Aluminum has traditionally been the most attractive material for fabricating battery boxes. With a high strength-to-weight ratio, relatively low cost, and high thermal conductivity, aluminum satisfies most of the requirements for an efficient battery box. Unfortunately, its impact absorption qualities are less than desirable.
When tradeoffs must be made, optimizing for crash protection is always the most important factor.
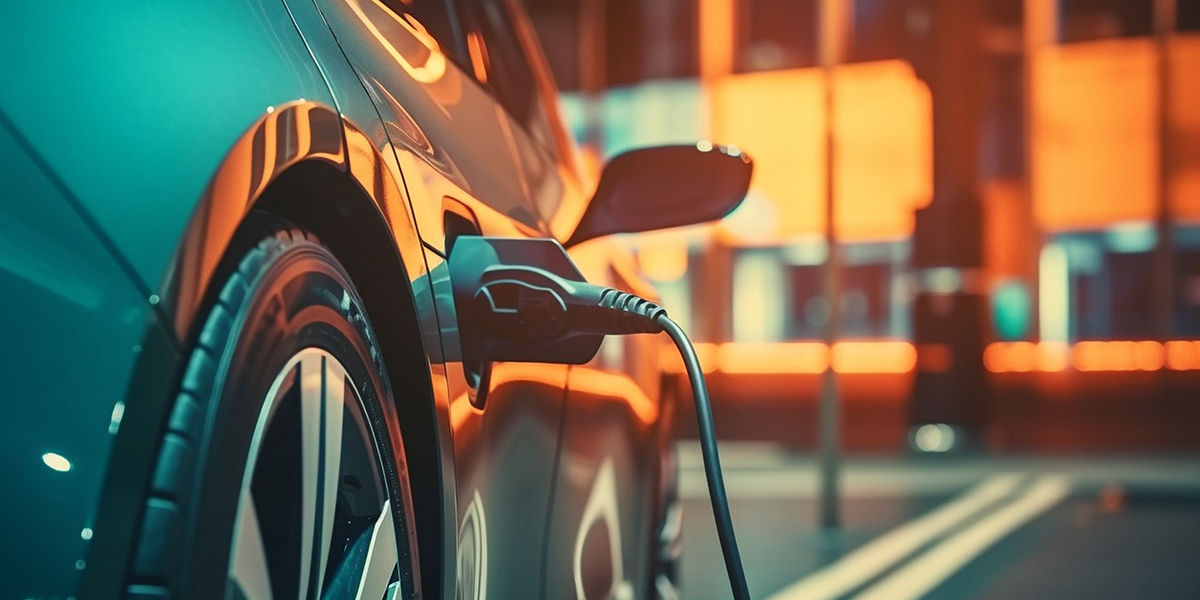
An electric car being charged. Image: Adobe Stock.
A MetaCORE®-enhanced battery box
Our team at Multiscale designed MetaCORE as a lightweight, energy absorbing material. It can be used to fabricate a better battery box by bonding with glass fiber-reinforced skins. These skins provide comparable puncture strength to aluminum and a smooth exterior surface. Without MetaCORE, the skins are non-load bearing and non-impact absorbing.
To demonstrate the crash protection capabilities of MetaCORE battery boxes alongside a simple aluminum counterpart, we conducted a drop test. Watch the video below to see how each box compared.
The high volatility of active battery cells makes them unsafe for experimental impact testing. Rather than risking an explosion or uncontrolled fire, we filled our battery boxes with ceramic payloads. Any cracks to the delicate ceramic gave us a good idea of the impact forces being felt within the walls of the box.
Thermoplastic composites compared to standard aluminum
Two thermoplastic MetaCORE battery boxes made of HDPE and PETG, as well as an aluminum box for reference, were subjected to repeated testing with up to 3.6 kN of load (about 810 pounds-force). Throughout the successive drop tests, the aluminum box crumpled and began to intrude onto the payload. The thermoplastic composite MetaCORE boxes were able to dissipate energy by elastically “bouncing” the weight.
After testing, we opened the boxes and inspected the ceramic payloads for damage. The ceramic articles in the MetaCORE battery boxes had a significantly higher survival rate than those in the aluminum box. Additionally, the boxes themselves were nearly unscathed and prevented any intrusions into the cavity.
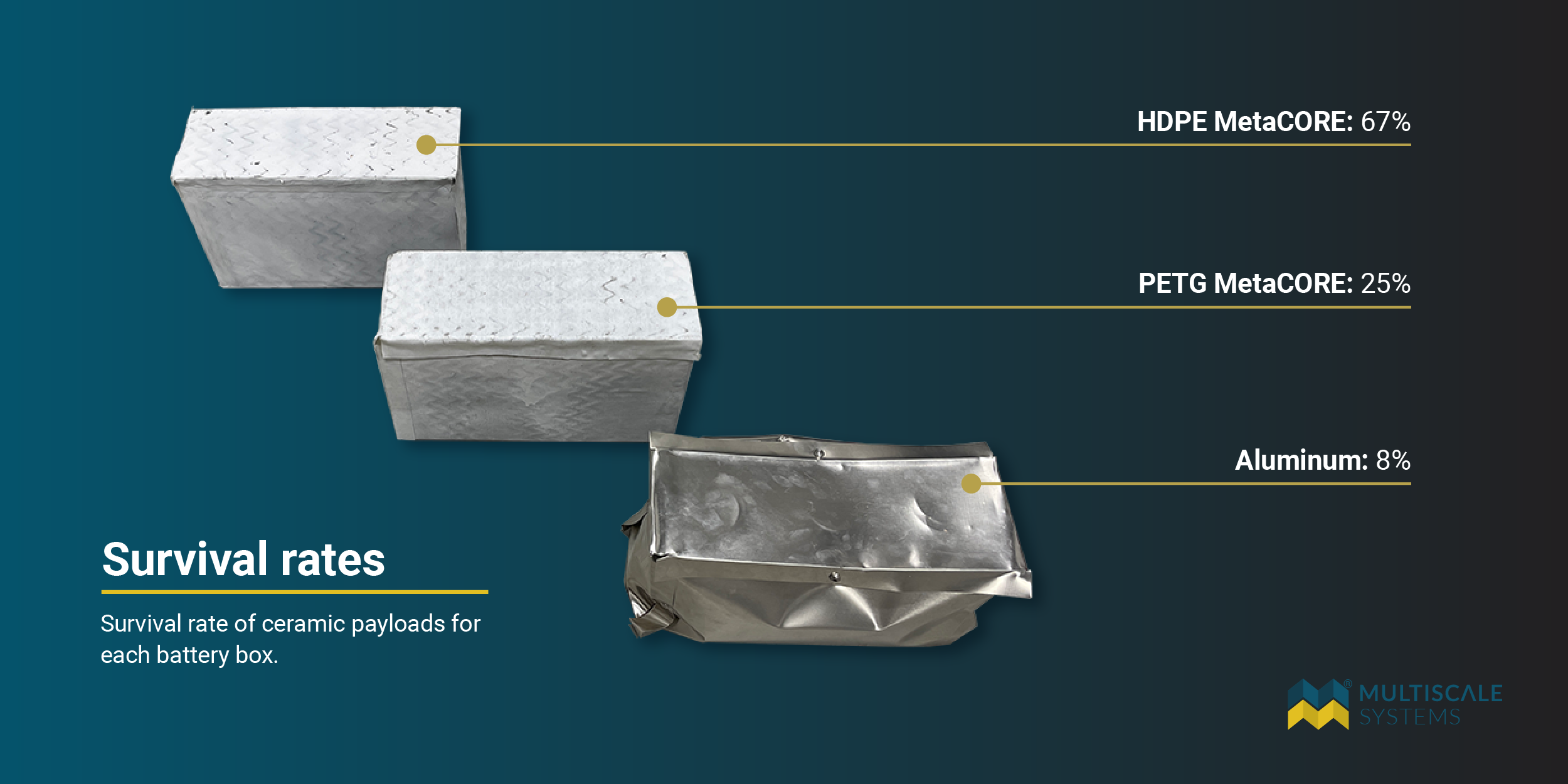
Survival rates of each battery box’s ceramic payload: HDPE MetaCORE 67%, PETG MetaCORE 25%, Aluminum standard reference 8%. Image: Multiscale Systems.
Making battery boxes smaller and lighter without sacrificing safety
MetaCORE can improve the safety of electric vehicles by increasing energy absorption to protect batteries, but impact mitigation is not the only purpose of a battery box. Lightweight battery boxes are multi-piece assemblies with dedicated components for thermal management, electronics, and structural systems. These subsystems each have separate, but necessary, functions for safe operation.
Electric vehicles can become more efficient if battery boxes are made smaller and lighter, but no singular feature of the current battery enclosure design can be removed without introducing safety concerns.
Part consolidation using MetaCORE
Rather than eliminating components, MetaCORE combines multiple battery module components into one system.
How? MetaCORE geometry includes continuous 6 mm (0.236 in) to 10 mm (0.394 in) channels that run laterally through the walls. These channels can be utilized to integrate a thermal management system directly into the crash protection element of the battery box.
By using existing elements in the energy absorber as a cooling channel, MetaCORE removes the need for separate parts dedicated to singular tasks while still possessing the necessary safety features. This part consolidation reduces mass and volume, allowing for a lighter, more compact, and overall, more efficient vehicle.
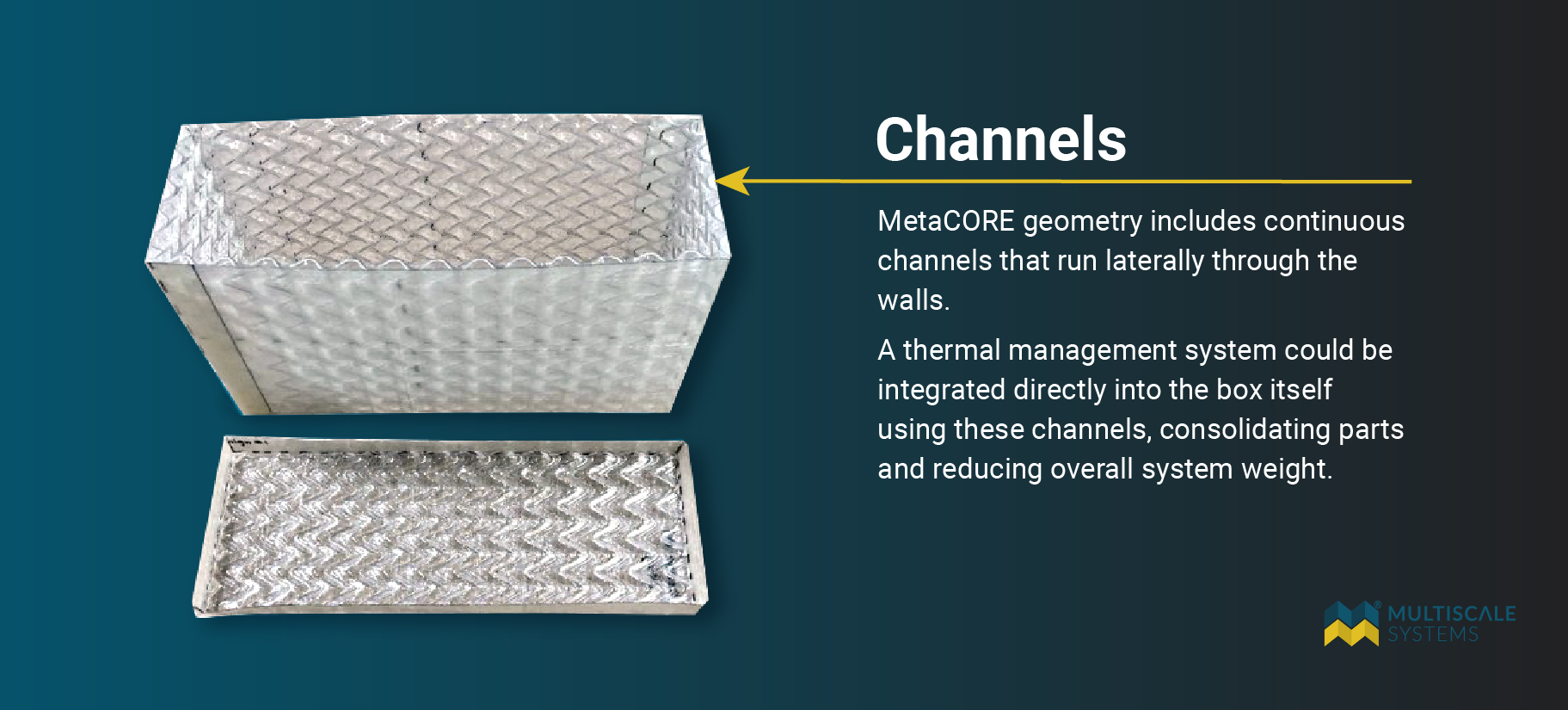
MetaCORE geometry includes continuous channels that run laterally through the walls. A thermal management system could be integrated directly into the box itself using these channels, consolidating parts and reducing overall system weight. Image: Multiscale Systems.
Thermoplastic MetaCORE | Aluminum | |
---|---|---|
Lightweight | ✓ | ✓ |
High strength-to-weight ratio | ✓ | ✓ |
Relatively low cost | ✓ | ✓ |
High thermal conductivity | ✓ | ✓ |
High impact absorption | ✓ | |
Part consolidation for reduced mass/volume | ✓ |
Electrifying the future
The multi-functionality of MetaCORE in battery box modules eliminates extraneous material, lowers overall weight and volume, and simplifies construction all while improving upon the crash protection capabilities of a standard aluminum battery box.
A better battery box expands the possibilities for electric transportation. Beyond cars, battery boxes are necessary implementations for electric trains, semi-trailers, and eventually electric vertical takeoff and landing (eVOTL) aircraft. Increased efficiency and safety of battery boxes will help battery-powered vehicles overtake combustion engines as the standard and ultimately move us toward a more sustainable future.
Latest Lab Notes
News /
July 18, 2025—Multiscale will engineer functionally-graded alloys tailored for molten salt and liquid metal environments, leveraging its hybrid manufacturing systems to produce nuclear-grade material performance.
News /
March 11, 2025 – Multiscale Systems to showcase cutting-edge industrial innovation during StartUp Week Worcester 2025.
News /
Multiscale Systems receives Massachusetts manufacturing award in recognition of outstanding leadership skills in the manufacturing industry.