Composite sandwich panels: A balance of weight and strength
If you’ve ever wondered how spacecraft, airplanes, race cars, and even your DIY furniture or cardboard box padding manage to be both lightweight and rigid, the answer lies in the composite sandwich panel. These engineered structures consist of two thin, stiff skins bonded to a lightweight, thick core, creating a sandwich-like configuration.
The beauty of sandwich panels is that they can serve as load-bearing elements while offering exceptional strength and stiffness at minimal weight and cost. In this post, we’ll explore why sandwich panels are widely used in various applications and discuss MetaCORE, our flagship metamaterial composite, and why it makes a superior panel.
The advantages of sandwich panels
Sandwich panels have gained popularity across industries due to their unique set of advantages, including their excellent stiffness-to-weight ratio. When compared to traditional I-beams or sheet-and-post structures, sandwich panels offer superior rigidity while keeping weight to a minimum. This property is crucial across industrial applications, including the aerospace and automotive sectors, where reducing weight is essential for achieving maximum speed and fuel efficiency.
However, sandwich panels are not limited to high-performance applications alone. They find their way into everyday items such as DIY furniture, cardboard box padding, and building construction materials. The reason for their ubiquity is the ability to create lightweight yet strong structures economically.
Understanding sandwich panel design
To appreciate the benefits of sandwich panels it’s essential to understand their design principles. A key parameter in estimating the performance of a composite sandwich panel is its flexural rigidity, which determines its resistance to bending or deformation. The flexural rigidity can be approximated as the product of the Young’s modulus of the skin, the thickness of the skin, and the thickness of the core:
Flexural rigidity = (Young’s modulus of the skin) x (thickness of the skin) x (thickness of the core)2
On the other hand, the weight of the sandwich panel depends on the density of the skin, the thickness of the skins, the density of the core, and the thickness of the core.
Weight = (density of skin) x (thickness of two skins) + (density of core) x (thickness of core)
Comparing these equations, we can see that the stiffness of a sandwich panel can be significantly increased without adding much weight (Figure 1). This scaling of stiffness-to-weight ratio is the defining characteristic that makes sandwich panels so versatile and valuable in a wide range of applications.
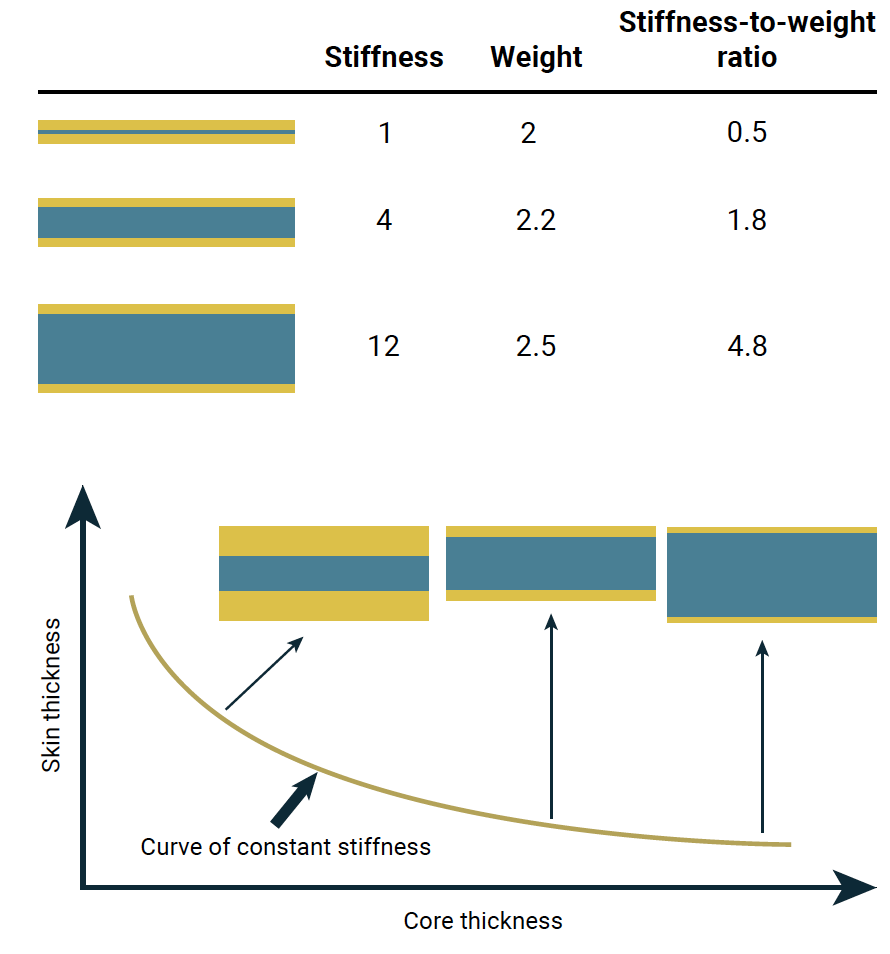
Figure 1: (Top) A sandwich panel increases its stiffness-to-weight ratio ratio by separating high stiffness skins with a low weight core. The benefit is to retain bending stiffness of the overall panel while keeping its weight low. (Bottom) Since this is a composite (the skins and core are different materials), there are many ways to construct a panel with the same stiffness.
The MetaCORE difference
While sandwich panels offer remarkable performance, predicting their strength and failure points can be challenging due to the complexities of non-linear material behavior. However, Multiscale Systems has developed a metamaterial composite – MetaCORE – for sandwich panel cores that promises to take panel design to the next level.
MetaCORE introduces a novel approach by reimagining the structure of the sandwich panel’s core. Traditional open-cell foam cores, such as PUR, XPS, and EPS, resemble tiny truss networks at the microscale. Consequently, their strength is determined by a “bending-dominated” mechanical response, resulting in a shear strength proportional to the effective density raised to the 3/2 power.
MetaCORE, on the other hand, employs intersecting polygons as its cell structure, deviating from the truss network configuration. This structural innovation leads to a “stretching-dominated” mechanical response, resulting in a shear strength proportional to the effective density. Similar arguments can be made for the stiffness and yields strength, and the results can be summarized as:
Here, E is the base material’s Young’s modulus, ρ is the density of the base material, and ρc is the density of core material (either foam or MetaCORE). To build a failure mode map, we’ll consider three possible ways a composite panel can fail in 3-point bending: yielding of the skin, wrinkling of the skin, and shearing of the core.
These scenarios assume the skin and core stay perfectly bonded at the point of failure. Calculating the failure loads and summarizing the results in a table gives:
The variables b, c, t, and L are dimensions of the panel (Figure 1). The modulus Ez is the Young’s modulus of MetaCORE in the panel’s normal direction, the modulus Es is the Young’s modulus of the skin, and the strength σs is the yield strength of the skin.
Comparing sandwich panel performance with failure mode maps
The failure loads do more than just estimate the maximum force a sandwich panel can withstand. These equations can be used to draw a map for how panels of various sizes and cores of various densities will perform (Figure 2). The boundaries of the map are determined by setting the various failure modes equal to each other and solving for how ρ/ρc depends on t / L.
Comparing two sandwich panel designs allows an at-a-glance understanding of the benefits of MetaCORE (Figure 2). The first design is a steel-skinned HDPE foam core common in semi-trailer construction. The second design is an equivalent sandwich panel with HDPE MetaCORE. Notice the smaller region where core shear is the primary culprit for failure. This change is attributable to MetaCORE’s large shear strength. The larger design space for failure by skin yielding is preferable, since the skins tend to be the strongest element in the panel.
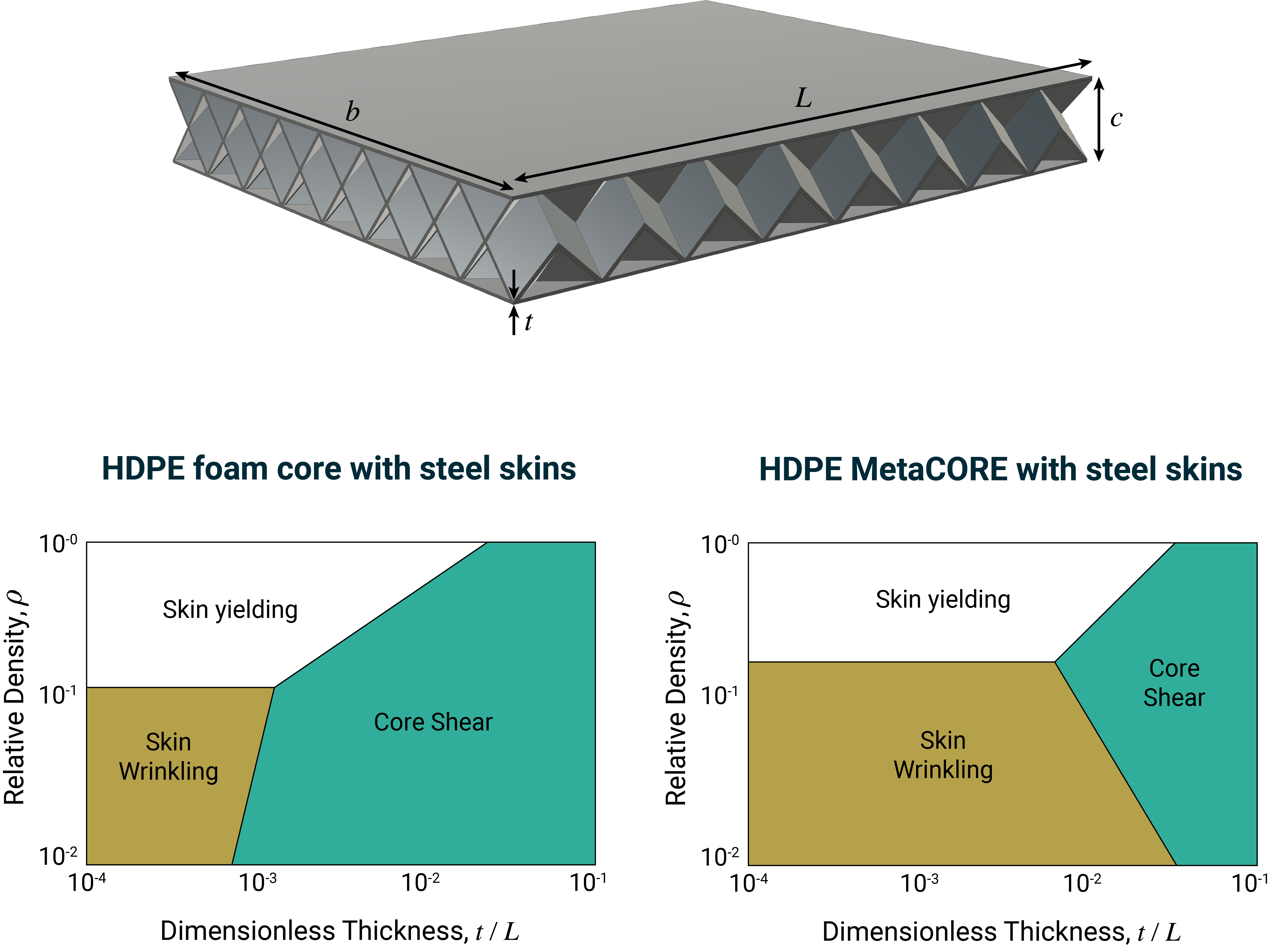
Figure 1: Making sandwich panels. (Top) Image of a MetaCORE sandwich panel labeling various key dimensions. (Bottom) Failure modes calculated for steel skinned HDPE foam core sandwich panels compared to MetaCORE sandwich panels with the same skins. The weakest part of the panel is generally the core, and thus core shear is the largest contributor of failure. The enhanced mechanical properties of MetaCORE lead to a subdominant core shear failure mode, and a better overall panel design.
Advancing sandwich panel technology
MetaCORE’s unique design offers several advantages over traditional open-cell foam cores. The stretching-dominated mechanical response of MetaCORE enables sandwich panels to achieve higher stiffness for a given weight. This breakthrough in material design enhances the load-bearing capacity and structural integrity of the panels, making them even more reliable and versatile.
MetaCORE’s improved mechanical behavior also allows for better prediction and analysis of failure modes in sandwich panels. By constructing a failure mode map, engineers can identify potential weak points and areas prone to delamination or cracks. This knowledge empowers designers to optimize the panel’s geometry and material selection, leading to more robust and durable structures.
Applications of MetaCORE sandwich panels
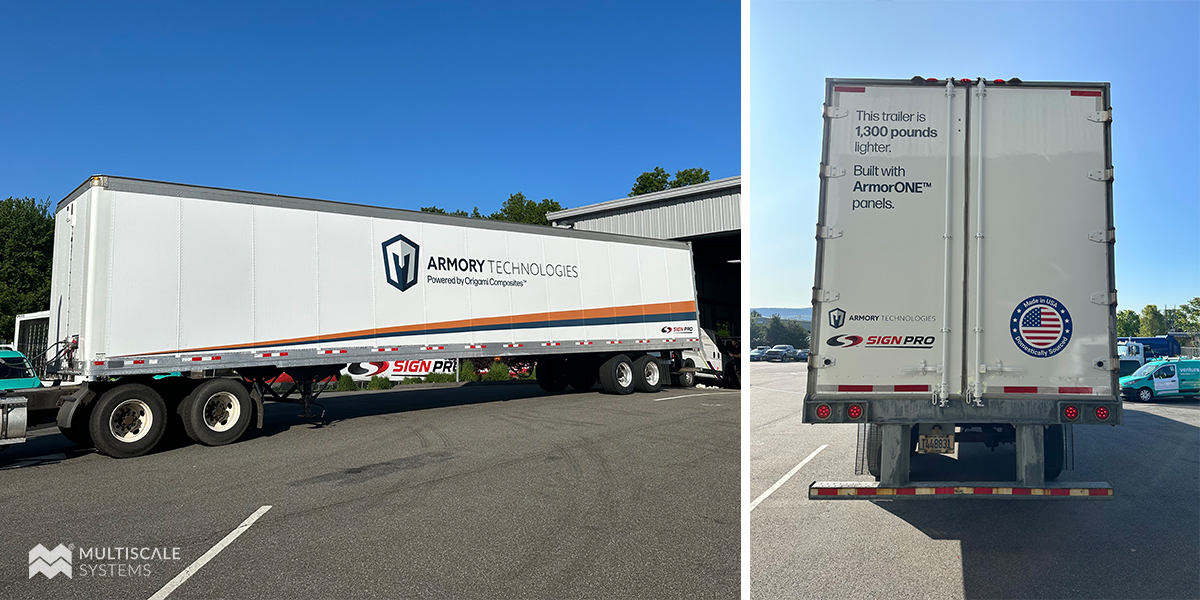
Image: MetaCORE is being used in Armory Technologies’ semi-trailer panels. This trailer is 1,300 lb lighter than if it used industry standard foam HDPE panels.
MetaCORE sandwich panels hold immense potential for various applications across industries. Their enhanced stiffness-to-weight ratio makes them ideal for aerospace and automotive sectors, where lightweight yet rigid structures are paramount. By incorporating MetaCORE sandwich panels, spacecraft can achieve greater maneuverability and fuel efficiency, while race cars can enjoy improved handling and speed.
In the construction sector, MetaCORE panels’ lightweight nature, combined with exceptional strength and rigidity, allow for faster and more cost-effective building construction. From housing projects to temporary structures, MetaCORE sandwich panels offer a sustainable solution that balances performance and affordability.
And in transportation, MetaCORE is already being used in panels for semi-trailers. Lighter trailers are able to haul more cargo, save on fuel, and reduce their carbon emissions.
A strong foundation for the future
Composite sandwich panels have become an indispensable part of modern engineering and manufacturing. Their lightweight, rigid nature makes them suitable for a wide range of applications, from cutting-edge aerospace technology to everyday commodities. With MetaCORE’s groundbreaking design, sandwich panels have reached new heights of performance, delivering enhanced stiffness, and improved structural integrity.
Working with MetaCORE: A Design Guide
For more in-depth information on using MetaCORE, including sandwich panel applications, check out Working with MetaCORE: A Design Guide (PDF, 13 MB).
Related Posts
Latest Lab Notes
Press Release /
WORCESTER, Mass. (July 12, 2024) – Multiscale Systems to build new facilities, expand advanced manufacturing capabilities, and bring jobs to Worcester with grant investment.
News /
Multiscale Systems moves on as a finalist in the Department of Energy's Heliostat Prize.
Press Release /
WORCESTER, Mass. (November 20, 2023) – The U.S. Department of Energy has announced Multiscale Systems as one of nine semifinalists in their American-Made Heliostat Prize. The prize is designed to accelerate technology innovation of selected heliostat components.