Composites can be confusing – what are they and how are they useful? Can you use them to make metamaterials? And importantly, we’ll explore the thermosets versus thermoplastics debate – and talk about which side we land on and why.
The word “composite” contains a lot of hidden information, and determining what kinds of composite materials are right for certain applications is a big part of the engineering process. In this article we’re going to talk in general about the types of composite materials out there, and discuss in detail the difference between two common types of composites: thermosets versus thermoplastics.
We’ve talked about the distinction between composites and metamaterials before, and how both can be used to design strong, lightweight parts for a variety of applications. What’s stopping us from making metamaterials out of composites? Nothing! In fact, we often use composite materials to create metamaterials, adding an extra layer of mechanical strength to the parts that we design.
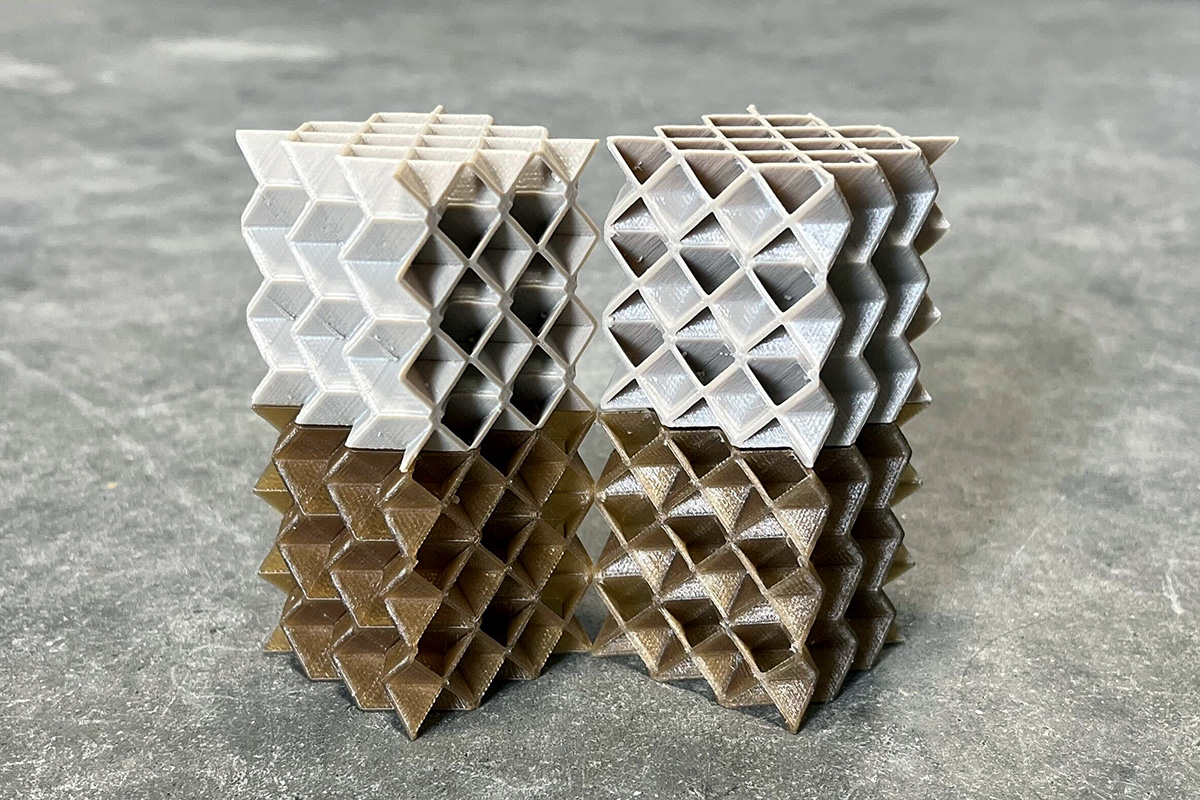
Thermoplastic composite metamaterials. PEEK is a thermoplastic commonly used at Multiscale to produce 3D-printed metamaterial prototypes. Shown here are pre-annealed (darker) and post-annealed (lighter) examples.
What are composites, exactly?
Before we jump into the difference between thermosets and thermoplastics, what are composites, anyway? Composites are simply a combination of two or more materials that are bonded together, with resulting properties that are more than the sum of their parts. The most common composite material made by humans is probably concrete, which consists of aggregate and cement (basically just loose rocks and a binding slurry to hold it all together).
Naturally occurring composites also exist, including wood, bone, teeth, and shells. An important distinction between a composite and a mixture or solution is that each component retains a distinct identity after forming. A solution is when the two parts are no longer distinguishable, like when sugar dissolves in your coffee or salt dissolves into boiling water.
Fiber-reinforced composites
Composites in the news are usually in the context of aerospace technology or some fancy new bicycle, sports car, or golf club. In all of these scenarios, high strength, high stiffness, and low weight are key engineering objectives for making a better widget. Usually the composites in these kinds of applications are fiber-reinforced polymers. In these cases, the two materials making up the composite are “fibers” and a “polymer matrix”.
Fiber-reinforcement is used to instill a high tensile stiffness and strength. Long, thin objects are naturally strong in tension, but weak in compression. It takes a lot more force to snap a string than to simply squish it under compression. To make up for this weak compressive strength, a polymer matrix binds the fibers together, resulting in a stiff, strong, lightweight material. In the schematic below an example of a chopped fiber composite is shown. More ordered composites are possible, and they range in their capabilities.
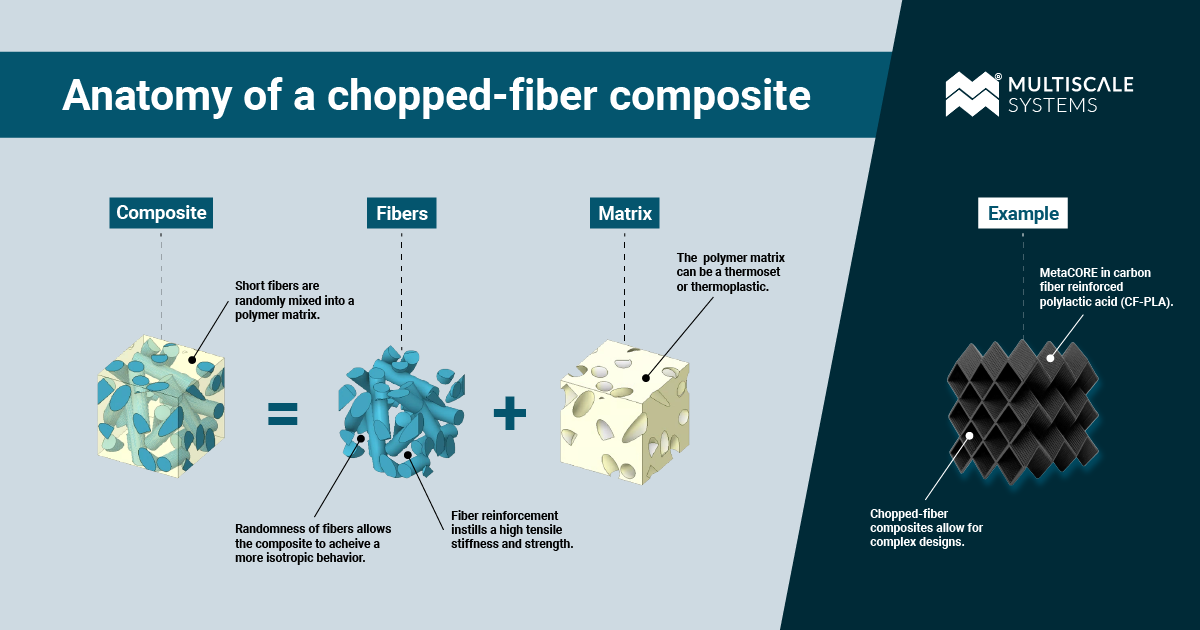
The anatomy of a chopped-fiber composite material. The fibers are short, and randomly mixed in with the “swiss cheese” of the polymer matrix. The random-ness of the fibers leads to a more isotropic behavior than unidirectional composites but cannot achieve the same ultimate strength. On the other hand, it is easier to work with chopped fiber composites. This type of chopped-fiber composite allows for complex designs like MetaCORE to be created with ease; An example of a carbon-fiber reinforced polylactic acid (CF-PLA) MetaCORE sample is shown here.
The importance of fiber arrangement and orientation
The arrangement of the fibers within the matrix determines the stiffness and strength of the composite, but it can also make them harder to work with. For example, the strongest fiber-reinforced composites are unidirectional (UD) with a high ratio of fiber to matrix. These composites are very strong in one direction, so if you need to make a part that is strong in many different directions, then you need to have the know-how and the equipment to arrange those UD composites.
To make more complex parts, it might be easier to use a chopped fiber composite. While chopped fiber composites are more isotropic, they’re typically not as strong as UD composite due to a different ratio of fiber to matrix. An intermediate between highest performance and greatest design flexibility is a woven fiber-reinforced composite.
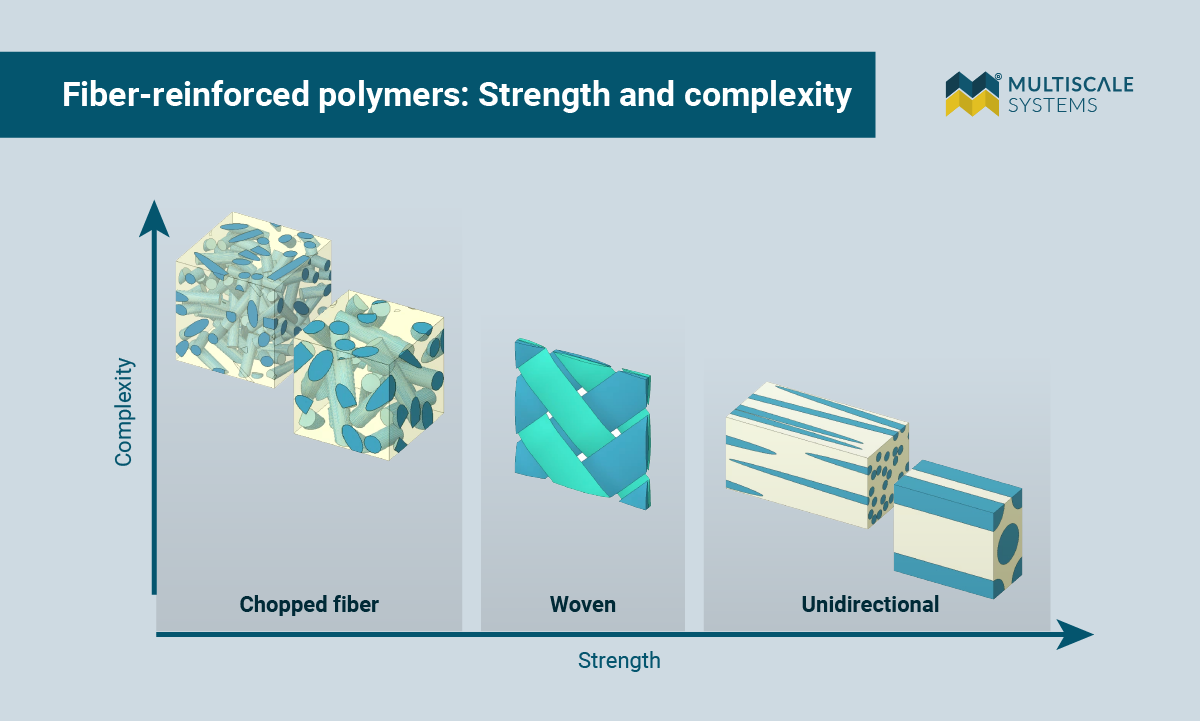
The range of strength and complexity of fiber reinforced composites. Schematics are shown here for representative units of UD, woven, and chopped fiber composites. The strongest composites tend to be UD tapes, with fibers pointing primarily in one direction, but ranging in their organization and how much of the total volume they take up. Woven composites are a little weaker than UD tapes, because they tend to have smaller ratios of fiber to polymer, but they are woven like a fabric to provide enhanced flexibility. Chopped fiber composites lack the high strength of UD composites, but are easily processed and can be used in a variety of molding applications.
Polymer matrix: Thermosets
So far we’ve mentioned the importance of fiber arrangement and orientation, but we haven’t said much about the matrix. The polymer matrix in a fiber-reinforced composite is usually either a thermoset or a thermoplastic. Woven glass fiber with a thermosetting resin is often used in the manual construction of boat hulls, for example, while higher strength carbon fibers are used in aerospace applications.
A thermosetting polymer resin is typically a liquid at room temperature, which makes it easy to work with since it can be painted onto the reinforcing fibers or infused using a vacuum bag. Although it starts as a liquid, when it is cured at a higher temperature it hardens irreversibly through chemical cross-linking. This hardening happens because the polymers that make up the resin chemically bond and cannot be undone. The phrase “you can’t unboil an egg” comes to mind (egg whites are also composed of thermosetting polymers, but don’t try to make a boat from them).
Polymer matrix: Thermoplastics
Thermoplastic composites are also composed of fibers and a matrix, but the matrix is a polymer that does not undergo an irreversible chemical change when heated and cooled. Instead, thermoplastics soften and melt when heated, allowing the material to be molded and formed, and then as the part cools, the matrix stiffens and re-solidifies. This kind of plastic is often used in thermoforming and injection molding and is used to make everything from car parts to yogurt containers.
This video shows thermoplastics being used to construct an aircraft fuselage, demonstrating that even large-scale parts are capable of being manufactured with thermoplastic composites.
Which is better? Thermosets vs thermoplastics
There are pros and cons to both. Most aerospace composites are still thermosets, despite decades of thermoplastic evangelism. Thermosets are better suited for higher temperature operating conditions since they have been irreversibly cured and thus won’t melt or soften at high temperatures. Thermosetting resins also tend to be cheaper than thermoplastics and are traditionally made into larger parts because of the ease with which the processing and curing can be done on larger molds.
The major advantages thermoplastics have over thermosets are improved impact resistance, reversibility, and recyclability. Thermoplastics composites have faster processing times since they aren’t required to cure, which make them attractive for applications that need a high volume of production, like the automotive and transportation industries, which have traditionally used aluminum for lightweight manufacturing.
However, thermoplastics are difficult to impregnate with fibers since they must be heated above their melting point before they soften, which often requires special equipment and tooling. Thermoplastics have high fracture toughness, low flame, smoke and toxicity ratings, and can be stored at room temperature (thermosets often need to be stored in a freezer to prevent curing while on the shelf). Overall, the largest benefits for thermoplastic composites can be summarized as “aluminum rates with carbon-fiber weights”.
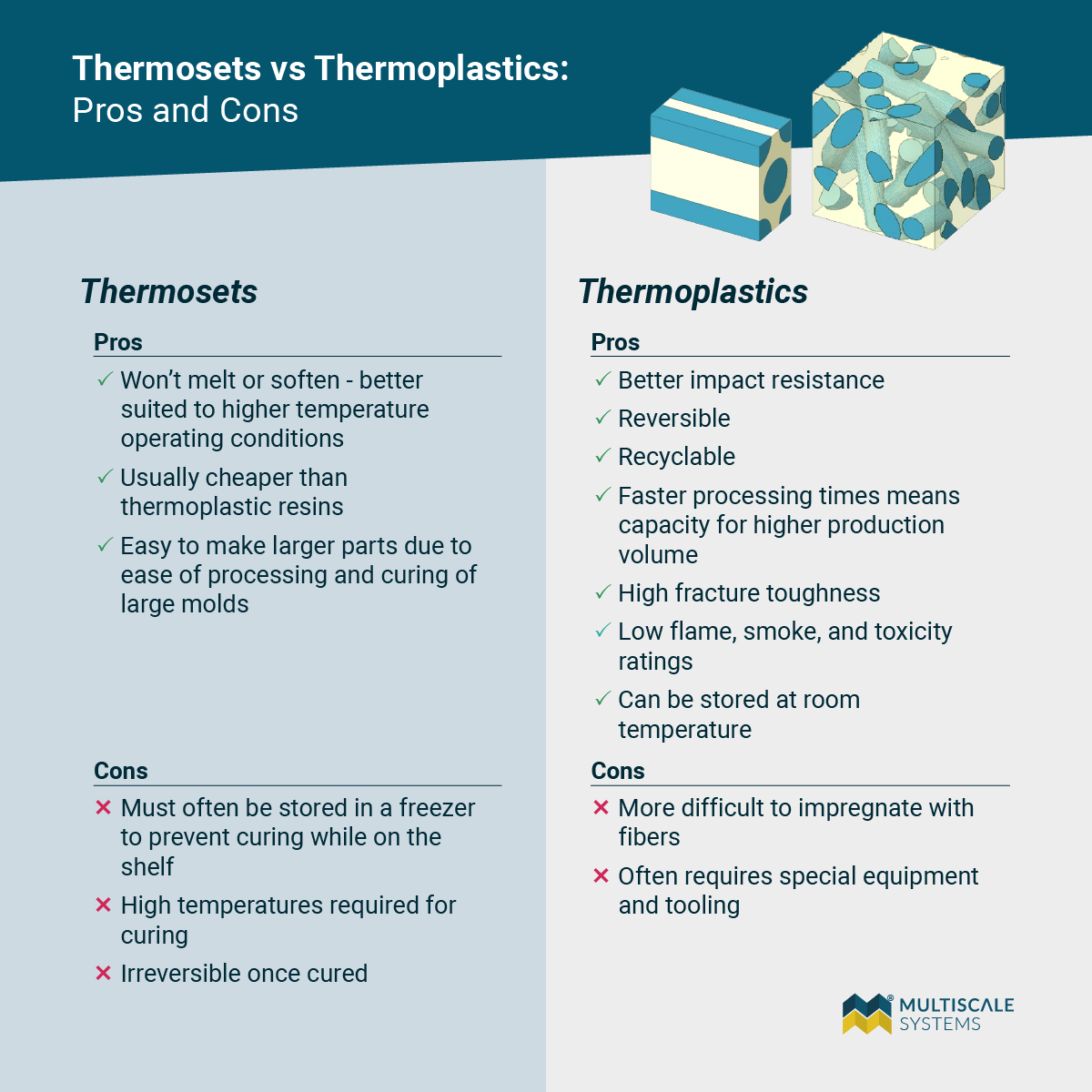
Thermosets versus Thermoplastics: Pros and Cons.
MetaCORE, STaMPER, and additive manufacturing
Maybe it was clear that I’m biased from the list above, but at Multiscale Systems we tend to use thermoplastic composites. Fast processing times means that we can use continuous compression molding to create metamaterials from fiber-reinforced polymers with record speed. As mentioned above, the combination of fibers with a polymer matrix make a composite that is more than the sum of its parts, and it does this on a length scale that is bigger than molecules, but still pretty small (glass fibers in the materials that we use tend to have a diameter similar to human hair). Metamaterial engineering adds another length scale for extra functionality.
Starting with the materials selected for the fibers and matrix, then combining them into a thermoplastic fabric, these composites are then consolidated into a thin sheet with the appropriate structure before entering our beloved continuous compression molding machine STaMPER, which molds the heated composite into a metamaterial geometry – like MetaCORE – that adds structure and performance by folding the fabric without damaging the reinforcing fiber matrix. This process allows us to quickly manufacture thermoplastic composite parts using UD tapes or woven fabrics, maximizing the strength of the part by properly designing the part and mold tooling ahead of time.
Watch a timelapse of STaMPER in action:
We use quality UD tapes like Polystrand to achieve versatility and strength in our thermoplastic composite metamaterials, providing high volume fraction glass fiber with a variety of resins to allow for adaptability.
For more complex geometric parts that require high temperature resilience we take advantage of additive manufacturing technology to create high strength thermoplastic composites from chopped carbon fiber reinforced polyether-ether-ketone (CF-PEEK). These parts not only have a higher temperature rating than traditional thermoplastics like HDPE, PETG, and PP, but they can be used to implement the high-performance metamaterial geometries designed at Multiscale for use in applications like geothermal energy generation and small satellite technology.
Our in-house additive manufacturing of CF-PEEK is enabled by 3DGence, whose Industry F350 fused filament fabrication system is used to prototype and fabricate parts like those shown below.
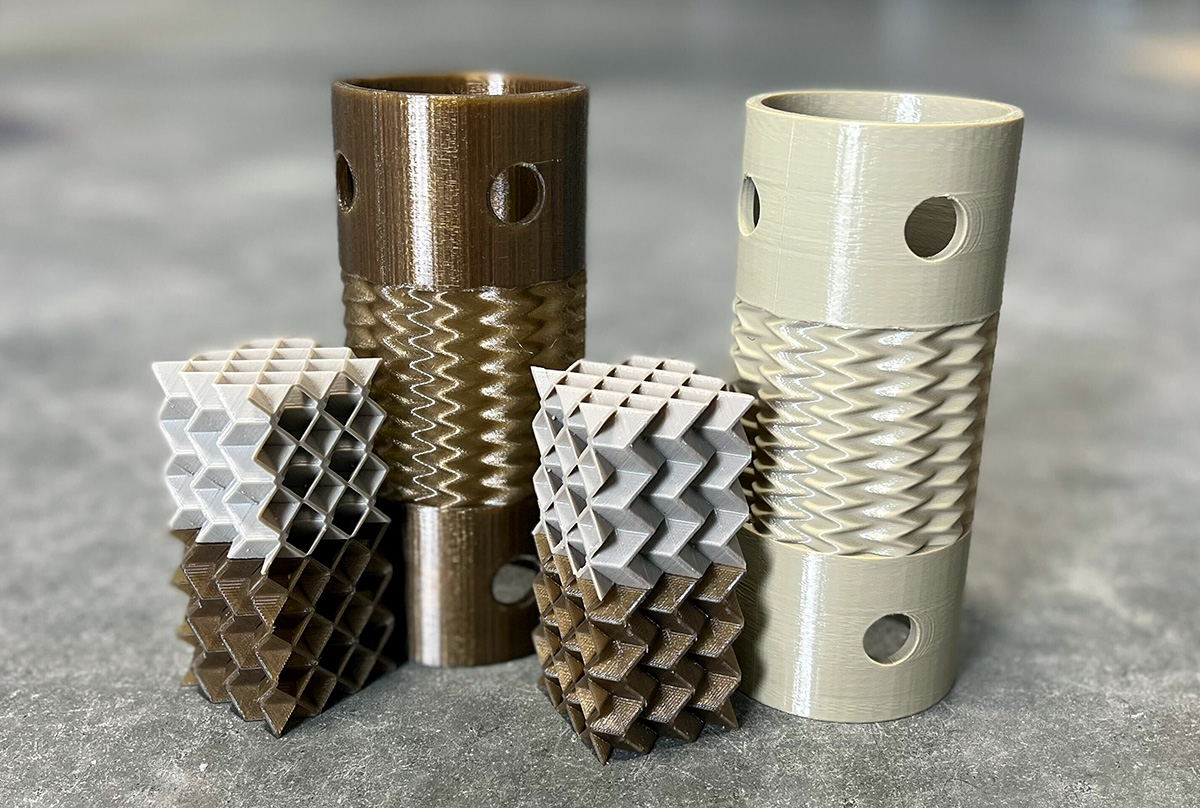
PEEK metamaterial prototypes. PEEK is a semi-crystalline, high-performance thermoplastic. The lighter parts shown here have been heat treated, or annealed, in order to decrease stresses caused during machining.
Thermoplastic composite metamaterials
Thermoplastic composite metamaterials open the door for a wide variety of applications, taking advantage of material capabilities and design complexity. Our flagship metamaterial, MetaCORE, is designed for isotropic mechanical response and high volume manufacturability, for use in a variety of different industries and products.
On the other hand, our geothermal energy metamaterial MetaTHERM was prototyped using additively-manufactured PEEK and allows complex parts to be fabricated that mitigate failure in geothermal wells. These are just a few of the myriad possibilities that thermoplastic composite metamaterials enable.
Would you like to work with Multiscale Systems on designing and building thermoplastic composite metamaterial for your applications? Get in touch! Contact us by email or call 1-855-955-7900.
Related Posts
Latest Lab Notes
Press Release /
WORCESTER, Mass. (July 12, 2024) – Multiscale Systems to build new facilities, expand advanced manufacturing capabilities, and bring jobs to Worcester with grant investment.
News /
Multiscale Systems moves on as a finalist in the Department of Energy's Heliostat Prize.
Press Release /
WORCESTER, Mass. (November 20, 2023) – The U.S. Department of Energy has announced Multiscale Systems as one of nine semifinalists in their American-Made Heliostat Prize. The prize is designed to accelerate technology innovation of selected heliostat components.