Research
Creativity, collaboration, and ingenuity are at the heart of our research.
Creativity, collaboration, and ingenuity are at the heart of our research.
Inventing advanced material solutions
We love solving complex, technical problems. It’s a habit formed by years of academic research and built upon by contracts with numerous federal and private organizations. Today, we develop solutions for industries including aerospace, energy, and defense.
Our interdisciplinary team of physicists, engineers, and builders achieves success through creative ideation and intense technical validation.
We leverage our expertise in metamaterial composites to design material solutions that not only solve important problems, but do so by providing unique advanced functionality.
Technology development
Our technology has been developed under contract with several federal and private organizations.
Federal Contracts & Awards
Thermoplastic Composite Heliostat Structures
Prize Finalist 2024 Department of Energy Learn More
Bimetallic Functionally Graded Materials for High-Temperature Corrosion Resistance
SBIR Phase I 2023 Department of Energy Learn More
Hydrogen Transportation and Storage Components Made with Metal Hybrid Additive and Subtractive Manufacturing
SBIR Phase I 2023 Department of Energy Learn More
Wire-Laser Metal 3D Printed Bearings for Extreme Environments
SBIR Phase I 2023 NASA Learn More
Metal Additive Manufacturing of Functionally Graded Materials for Roller Bearings in High Temperature Sodium Systems
SBIR Phase I 2022 Department of Energy Learn More
Contact-Free Metrology for Testing Metamaterial Quality
SBIR Phase II 2022 NIST Department of Commerce Learn More
Accelerated Aging of Lightweight High-Strength Mechanical Metamaterials
SBIR Phase I 2021 NASA Learn More
Additively Manufactured High-Strength Casing Connectors
Prize Semifinalist 2021 Department of Energy Learn More
Development and Application of Mechanical Metamaterials to Address Needs in Geothermal Technologies
SBIR Phase I 2020 Department of Energy
Ultra-Lightweight Mechanical Metamaterials for Mitigating Impacts and Crashes of Urban Air Mobility Vehicles
SBIR Phase II 2020 NASA Learn More
Lowering Hydro Costs with Mechanical Metamaterials
Prize Winner 2021 Department of Energy Learn More
Lightweight, Impact Absorbing JPADS for Air Drops
Prize 2020 xTechSearch Learn More
Ultra Low-Cost Mechanical Metamaterials to Enable Mobility and Interactivity for Cyber-Physical Devices
SBIR Phase I 2019 National Science Foundation Learn More
Partners and Accelerators
Our partners provide invaluable support and resources:
- Ansys
- Dawnbreaker
- FedTech
- Larta Institute
- Lever
- MassChallenge
- Massachusetts Clean Energy Center
- StartUp Worcester
Metamaterial composites
More than the sum of their molecules
Multiscale Systems is the expert in metamaterial composites, a structural material that unlocks advanced functionality that’s difficult or impossible to create with normal materials.
Metamaterials are common materials – like metals, polymers, and composites – formed into computationally generated, complex geometries. These geometries are tailored to each application, designed to provide enhanced performance and unique functionality.
Inspired by origami’s process of folding flat sheets into three-dimensional forms, metamaterial composites can be made using familiar manufacturing methods, such as additive manufacturing, thermoforming, and pattern transfer. Advanced functionality manifests through the unique combination of selected materials and patented geometric patterns.
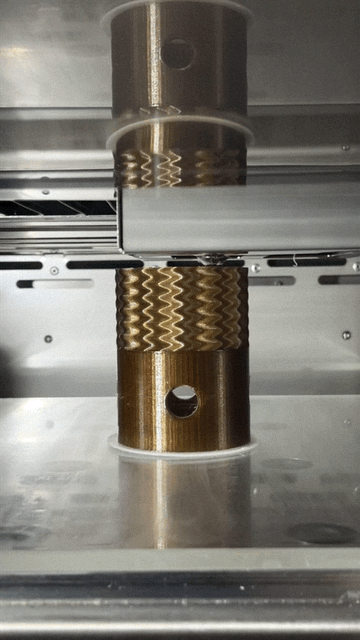
Metamaterial composite technologies
Created under contract with NASA and the U.S. Department of Energy, these technologies have been designed with specific application functionality.

MetaCORE®
Ideal energy absorber
Isotropic energy absorption
Lightweight
Mitigates sudden deceleration
Customizable crush strength
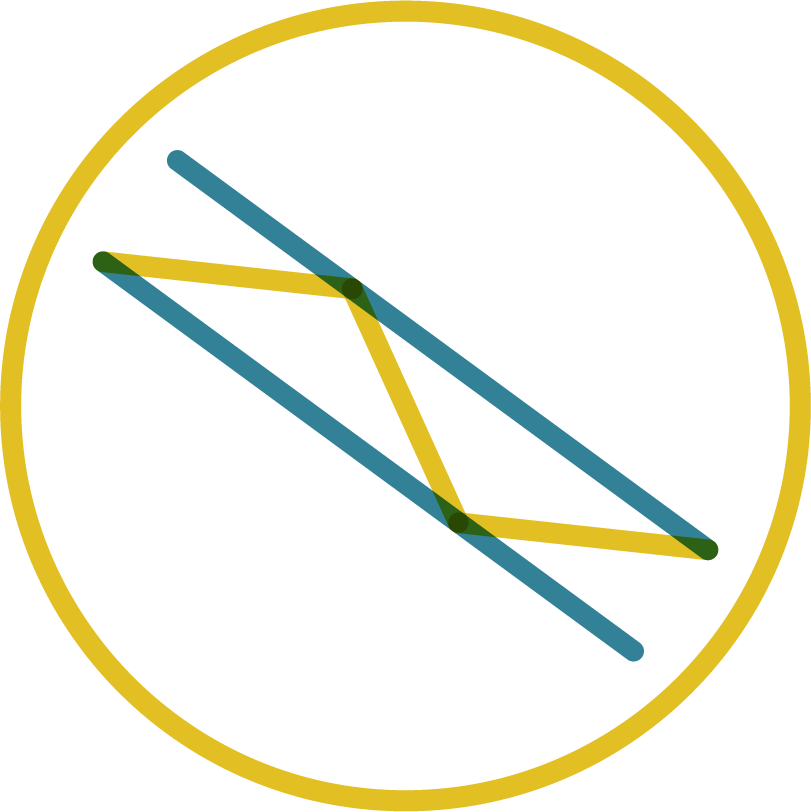
MetaCORE®-LD
Lightweight sandwich panel
Low density cores
High shear strength
Temperature regulation
Sustainable materials
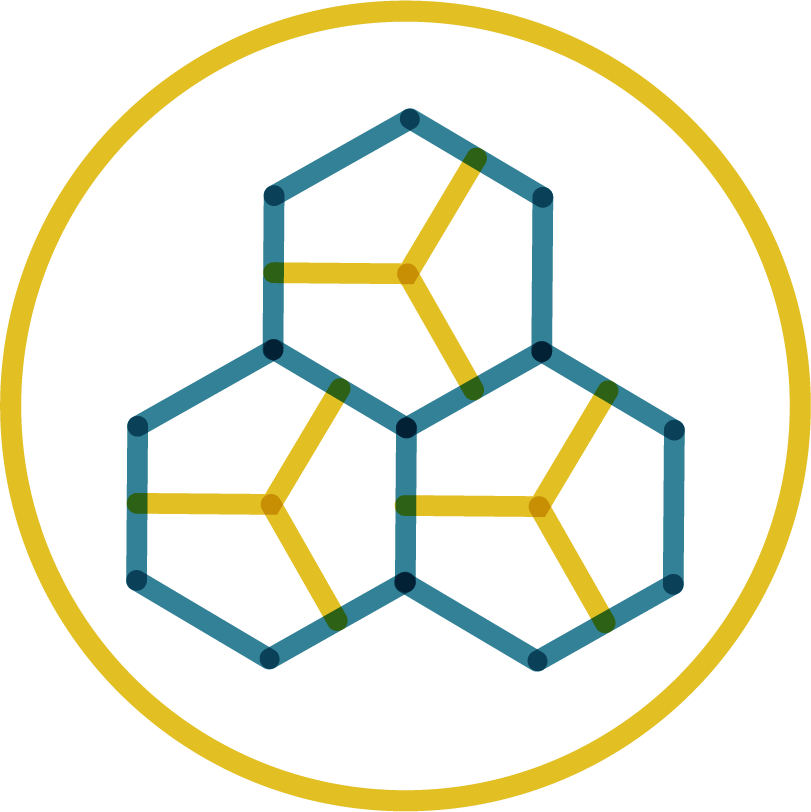
MetaTHERM®
Extreme environment survivability
Holds severe pressure differentials
Controls thermal expansion
Regulates temperature
Mitigates equipment failure
Technology development case studies
Dive deeper into our R&D through case studies. We examine lessons learned and insights gained while developing our technology.
In 2019, we won an NSF SBIR for development of mechanical metamaterials. What began as a general desire to do something with our metamaterial research evolved into a targeted commercialization strategy for MetaCORE-LD as an alternative lightweight sandwich panel for semi-trailers.
Safety is a big concern for UAMVs. NASA is proactively seeding the development of lightweight crash mitigation technology in preparation for this emerging mode of transportation.
The U.S. Army is modernizing its acquisition of disruptive technologies like our mechanical metamaterial solutions. Representatives from AFC and ASA(ALT) selected Multiscale Systems’ MetaCORE technology for acceleration through the xTechSearch program.
Achieving utility scale geothermal energy is bottlenecked by the cost of equipment failure in extreme downhole environments. New materials – like MetaTHERM – are required to unlock the potential of Enhanced Geothermal Systems (EGS).
In 2021, we received an SBIR contract from the National Institute of Standards and Technology (NIST) for the development of a contact-free optical metrology method to standardize the manufacturing of mechanical metamaterials.