What is thermoforming?
Thermoforming is a manufacturing process that involves transforming thermoplastic sheets into various shapes by applying heat, pressure, and molds. It’s a highly versatile process, allowing for the creation of a wide range of products with varying complexities – from simple packaging containers to intricate parts for the automotive or healthcare industries.
It begins with a flat thermoplastic sheet (if you’re wondering what a thermoplastic is, we have a blog article that explains just that). The sheet is heated until it becomes pliable, which is then placed over a mold. Force is applied, the sheet is stretched and conforms to the mold. Once cooled, the sheet keeps its shape and any access can then be trimmed.
It’s a fast and economical way to create all sorts of parts, especially compared to manufacturing processes like injection or blow molding.
Vacuum vs Pressure vs Matched-die
There are several thermoforming methods, with three of the most common being vacuum thermoforming, pressure thermoforming, and matched-die thermoforming.
Vacuum thermoforming
With the vacuum method, the pliable sheet is placed on a mold and then a vacuum pulls the sheet down into it. This thermoforming process uses a single mold to create the part.

Figure 1: In vacuum thermoforming a heated polymer sheet is placed on a mold which then applies a vacuum, pulling the sheet into full contact with the mold surface. After a predetermined amount of time the mold is released and the finished part is ready for trimming.
Using a single mold means less tooling, but it can also mean non-uniform wall thicknesses with the final shape, since the thermoplastic hits the top of the mold first and immediately starts cooling. The effect can be thicker “mountains” and thinner “valleys”. In some applications these differences may not matter, but if you’re looking for more precise thermoforming, you may want to consider the second option.
Video: An example of metamaterial composites being vacuum thermoformed on an industrial thermoforming line.
Pressure thermoforming
Pressure thermoforming involves air pressure being applied against the heated thermoplastic sheet, which pushes the sheet down into a mold cavity.
Matched-die thermoforming
With matched-die thermoforming, two molds – one on top and one on bottom – are used to apply pressure. The pliable sheet is placed between the two molds and they are pushed together, creating the desired shape.
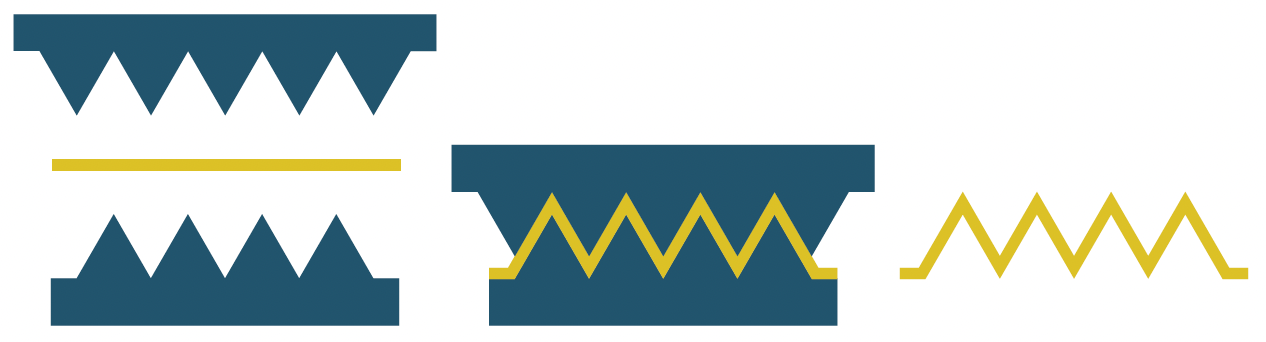
Figure 2: In matched-die thermoforming, two molds “sandwich” a heated polymer sheet to form the final part. Advantages over vacuum thermoforming include uniformity of wall thickness, but often more machinery and tooling is required.
This thermoforming method produces more uniformity when it comes to wall thicknesses, but will usually require more machinery and tooling to perform.
Video: An example of metamaterial composites being pressure thermoformed on our in-house rapid prototyping thermoforming machine.
Benefits of thermoforming
There are many benefits to thermoforming over other manufacturing methods including injection molding, blow molding, extrusion, and milling.
- Cost effectiveness: Thermoforming is a cost-effective method for producing plastic components. The tooling and equipment costs are generally lower, making it an accessible option for a wide range of industries. Larger sized components can also be produced easily.
- Rapid prototyping: Thermoforming allows for the quick production of prototypes and small batch runs. Combined with additive manufactured molds, designs can be tested and iterated quickly.
- Design flexibility: The versatility of thermoforming allows for intricate and complex designs, as well as simple shapes. Smooth curves and sharp angles can be replicated accurately.
- Material variety: Thermoforming can work with a board range of thermoplastic materials, each offering their own properties such as transparency, rigidity, and temperature range. Such variety enables manufacturers to select the best material for specific applications.
- Short production cycles: Thermoforming has relatively short production cycles, making it suitable for tight deadlines and responding quickly to changing market demands.
- Sustainability: Many thermoplastics, and excess materials created during the manufacturing process, can be reused and recycled, making thermoforming a good choice for a more sustainable manufacturing process.
There can be some drawbacks to thermoforming, one of which is the expense to produce the tooling. However, once made, a tool should last a very long time before needing to be repaired or replaced.
Applications
Because of thermoforming’s ability to produce parts in a variety of shapes and thermoplastics, it has a wide range of applications across many industries. Some common applications include:
- Packaging: Thermoforming is used to make packaging from trays and blister packs, to clamshells and inserts to hold consumer goods. Some examples of thermoplastics commonly used to create packaging include PET, polypropylene, polystyrene, PVC, PLA, and APET. Generally, these plastics are used because they offer transparency, are lightweight, and many are recyclable.
- Automotive: Thermoforming plays a vital role in the automotive industry by producing interior components like door panels, dashboards, and trim parts. Its cost effectiveness is particularly advantageous for high-volume production.
- Medical equipment: The medical industry uses thermoforming to produce sterile and single-use items like trays for surgical instruments and housing for medical devices.
- Consumer goods: Many everyday items like single-use cups, food containers, and cosmetic packaging are made using thermoforming due to its affordability and speed of production.
- Appliances: Appliance parts like refrigerator liners, oven doors, and dishwasher components can quickly and easily be made using thermoforming.
Thermoforming metamaterial composites
Metamaterial composites are structural materials with advanced functionality that’s difficult or impossible to create with normal materials. They can be made with materials like metals, composites, and thermoplastics and are formed into complex geometries. It’s these geometries that provide enhanced performance and unique functionality. At Multiscale Systems, our patented metamaterial composites can be used in a whole range of application in industries as diverse as aerospace, energy, and transportation.
Thermoforming offers an excellent manufacturing method for producing metamaterial composites. For example, MetaCORE cores are vacuumed thermoformed to create sandwich panels.
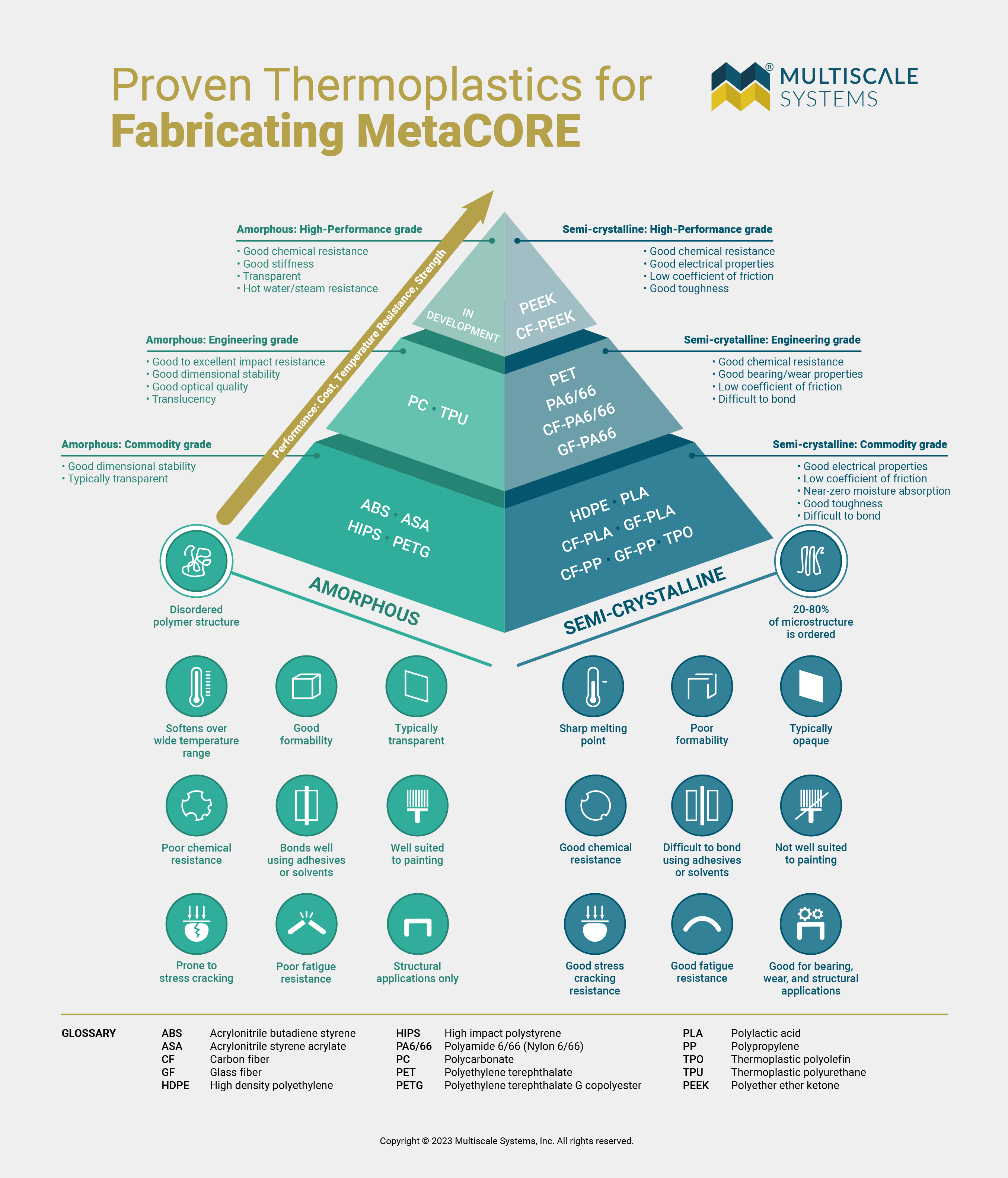
Image: Thermoplastics are ideal for thermoforming. This graphic includes information about the thermoplastics that have been proven for fabricating MetaCORE.
But first: Thickness variation from vacuum forming
Let’s discuss thickness various that occurs when vacuum thermoforming metamaterial composites. We use data like this to improve our products.
This information can also be found in our Working with MetaCORE: A Design Guide (PDF).
There are at least three important sources of thickness variation to identify and understand when working with thermoformed parts:
- Variation between the initial unformed sheet’s gauge and the final formed part’s wall thickness.
- Long length-scale thickness variations spanning the part.
- Short length-scale thickness variations in the formed walls due to the vertical draw.
For the first type of variation, a simple heuristic prediction can be made using the Areal Draw Ratio (ADR) of the part to determine how the final thickness differs from the initial gauge. The ADR computes the surface area of the mold face and compares it to the area of the unformed blank. The resulting ratio is the factor by which global thinning of the formed part can be anticipated.
For the second type of variation, independently controlled heating and cooling zones on the thermoforming equipment can be configured to offset this effect.
For the third type of variation, it’s important to understand that the nature of vacuum thermoforming leads to wall thickness variations that are ultimately unavoidable. As the heated material touches the cooler mold, it immediately begins to lose malleability and so the regions of the part that contact the mold first tend to have a larger thickness. This thickness variation can be predicted, but it’s more difficult since it’s dependent on several environmental variables.
With MetaCORE tooling, the cross-sectional thickness variations typically look like the following sketch (Figure 3), with thicker “mountains” on one side of the sheet and thinner “valleys” on the other. These differences can become important in a handful of specific applications.
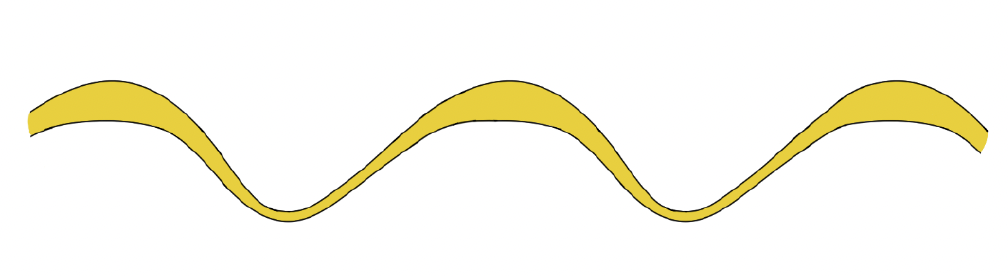
Figure 3: Schematic cross section based on MetaCORE of how wall thickness can vary in a thermoformed part. Areas higher up on the mold cool off sooner, and thus have a tendency to be thicker than parts lower in the mold.
The second and third types of wall thickness variations listed above are negligible in pressure forming thermoforming, compared to vacuum thermoforming. As such, parts made with pressure forming have more consistent thickness and are generally better for manufacturing high-performance parts.
ADR for thermoformed MetaCORE
Both the size and geometric complexity of a part will affect the overall thickness variations and quality of the metamaterial composite being formed. Since metamaterial composites are based on well-defined mathematical parameters, estimates for wall thickness variation can be made based on the geometry of the part.
Figure 4 below shows the ADR of MetaCORE sheets for different sizes and shapes. The ADR should ideally be as low as possible to mitigate wall thickness variation from sag, as well as the local variations associated with steep walls.
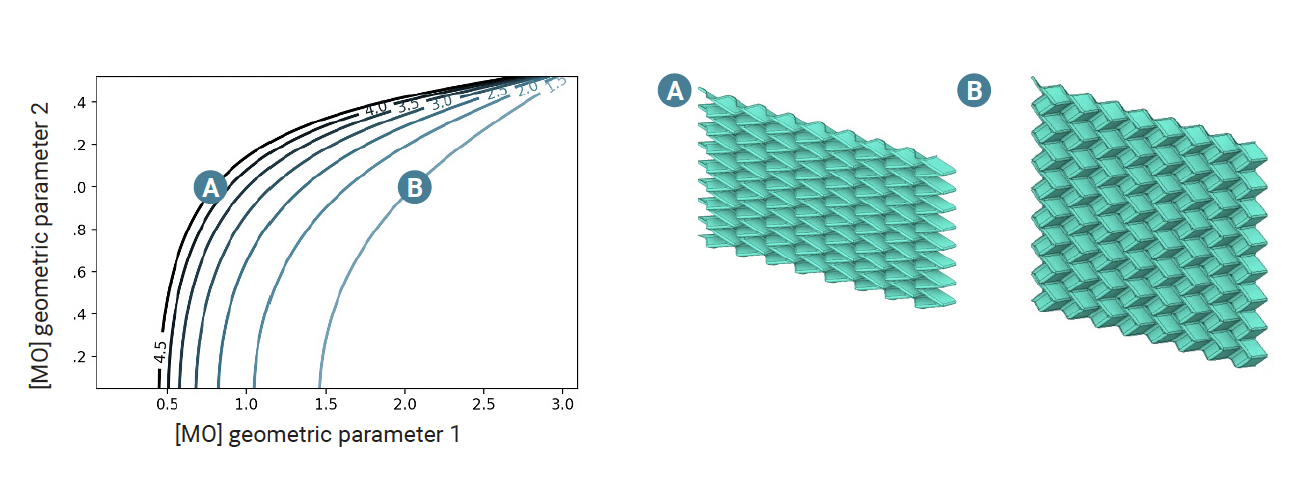
Figure 4: Left: a contour plot of ADR for a MetaCORE sheet. Different angles produce wildly different draw ratios. Right: rendering of the shapes from the contour plot with ADR of 4.5 and 1.5, respectively. (A) Has a steeper incline to the pattern, and as a result more surface area to form compared to (B). This change in draw ratio will lead to larger thickness changes in the final part.
ArmorONE™ panels: A thermoforming case study
As mentioned, an example of a thermoformed metamaterial composite is the core of ArmorONE panels (ArmorONE panels are sold by Armory Technologies – if you are interested in using a metamaterial composite in your next product, contact Armory Technologies).
ArmorONE panels come in several varieties, including steel skinned and advanced composite skinned versions. All have the same thing in common: a thermoformed, thermoplastic core. The type of thermoplastic used depends on the specific application of the sandwich panel.
ArmorONE panels have been used in semi-trailer and box truck construction, an ideal application due to being extremely light weight with an impressively high sheer strength.
By having thermoformed the cores, ArmorONE panels benefit from:
- Being produced in the U.S. by domestic manufacturers (thermoformers and resin producers)
- Offcuts and trimmings get reused
- Offering precision for core geometry
- Quick and economic production
- The same tooling used with a variety of thermoplastics
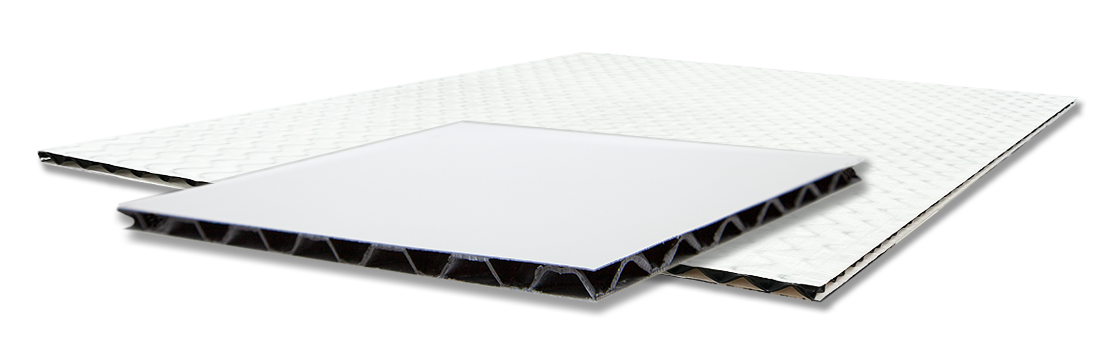
Image: Steel skinned and Advanced Composite ArmorONE panels from Armory Technologies.
Thermoforming leading the way
Thermoforming is a cornerstone of modern manufacturing, embodying innovation, versatility, and efficiency. It’s ability to transform plastic sheets into a diverse range of items influences how industries make products, from packaging to cars.
Its design flexibility, cost effectiveness, and rapid production cycles make it a go-to choice for both prototyping and high-volume production, underscoring its impact across the entire product lifecycle.
And as sustainability becomes ever more important, biodegradable and recycled plastics are well positioned to become ever more popular materials used in the thermoforming process.
Related Posts
Latest Lab Notes
Press Release /
WORCESTER, Mass. (July 12, 2024) – Multiscale Systems to build new facilities, expand advanced manufacturing capabilities, and bring jobs to Worcester with grant investment.
News /
Multiscale Systems moves on as a finalist in the Department of Energy's Heliostat Prize.
Press Release /
WORCESTER, Mass. (November 20, 2023) – The U.S. Department of Energy has announced Multiscale Systems as one of nine semifinalists in their American-Made Heliostat Prize. The prize is designed to accelerate technology innovation of selected heliostat components.